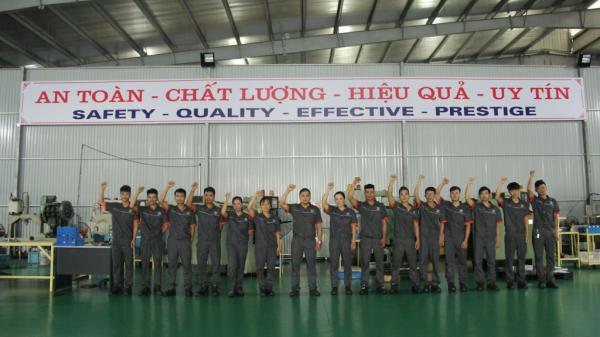
What is Precision Turning (CNC Turning)?
Precision turning is a machining method that uses the rotational motion of the workpiece combined with the linear motion of a cutting tool to create parts with circular shapes. In practice, CNC turning is a vital machining method with broad applications in various industries.
The engineer is operating the lathe machine
Applications of CNC Turning
CNC turning is essential to the manufacturing industry, enabling the production of highly precise and reliable parts. Turning techniques contribute to creating flawless products with superior accuracy. Below are primary applications of CNC turning methods widely used in modern mechanical machining:
Shaping Components
CNC turning is essential in machining, offering the precision and efficiency required to shape complex parts:
Creating Round, Rotational Shapes: The main function of turning, CNC lathes produce small, rotational parts such as shafts, cones, grooves, holes, and flanges with high precision—examples include automotive shafts, pump shafts, gears, bolts, and screws.
Producing Symmetrical Shapes: Beyond circular forms, CNC lathes can create axially symmetrical shapes, including cones, spheres, and ellipses.
Cutting Threads: CNC lathes precisely cut internal and external threads, handling intricate designs such as bolts, nuts, and pipe fittings.
Forming Grooves and Ridges: Lathes can also create various grooves and ridges, such as keyways, water drains, and alignment ridges.
Machining Large Parts: CNC lathes are also capable of accurately machining large components.
Machining Flat Surfaces
Flat surface machining is a key process in CNC turning, used to create flat surfaces on parts with high precision and smoothness. Its specific functions include:
- Creating flat surfaces for component assembly.
- Forming sealing surfaces to prevent liquid or gas leaks in joints.
- Machining flat surfaces for accurate positioning during manufacturing or assembly.
- Adding flat surfaces for decorative purposes.
Methods for Machining Flat Surfaces in Turning:
- Face Turning: Uses CNC turning tools with cutting edges perpendicular to the lathe’s main spindle to machine flat surfaces.
- Planing Turning: Employs tools with angled cutting edges relative to the spindle to create flat surfaces.
- Reaming: Involves reaming tools to achieve high-precision flat surfaces with a smooth finish.
Machining Grooves and Threads
Machining grooves and threads are two critical processes in turning, designed to create grooves and threads on components with high precision and efficient production. The specific functions of groove and thread machining include:
- Creating grooves for chip removal, which enhances machining efficiency and reduces tool wear.
- Forming grooves for accurate positioning during machining or assembly.
- Producing grooves for sealing purposes.
- Cutting threads for assembly with other components, ensuring necessary precision and tightness in joints.
- Creating threads for power transmission between parts, such as in screw shafts, lead screws, and nuts.
Cutting the Workpiece
The functions of cutting the workpiece in turning include:
- Removing excess material during machining.
- Achieving high precision.
- Increasing machining productivity.
- Saving material in the machining process
Some CNC turning products from Tân Hưng
Advantages and Disadvantages of Turning Machining Method
Advantages
The turning machining method has many outstanding advantages, making it a popular choice in the mechanical engineering industry. Lathes use advanced technology to ensure that products are machined with high precision, meeting the stringent requirements of modern industries. As a result, the machined products are durable and efficient in use.
CNC lathes can operate continuously at high speeds, increasing productivity and efficiency, which helps optimize time and costs. Additionally, flexibility is a noteworthy advantage of turning machining methods. Lathes can process various types of materials, including metals, plastics, wood,…
CNC lathes can machine complex parts with high precision and automation capabilities, which helps reduce machining time and increase productivity. Moreover, CNC lathes also minimize human errors in the precise machining process.
Disadvantages
Alongside these advantages, the turning machining method also has some drawbacks to consider:
Limited machining capability: The turning method is only suitable for machining parts with cylindrical or conical shapes.
Time-consuming setup: Programming a CNC lathe can be time-consuming, especially for products with complex structures.
The requirement for high skill level is also a disadvantage of the turning machining method. To operate a CNC lathe effectively and safely, operators need to possess a high level of skill and specialized knowledge in machining.
Tan Hung, with a highly skilled workforce and extensive experience, provides turning machining services using advanced CNC lathe systems, ensuring high precision and tailored to your specifications.
Contact with us
Call (+84)0976.189.965 to get started on your next project.